5 Simple Techniques For Alcast Company
5 Simple Techniques For Alcast Company
Blog Article
The Single Strategy To Use For Alcast Company
Table of ContentsThe Best Strategy To Use For Alcast CompanySome Ideas on Alcast Company You Need To KnowAlcast Company Can Be Fun For EveryoneLittle Known Facts About Alcast Company.Not known Details About Alcast Company Alcast Company Fundamentals ExplainedThe 9-Minute Rule for Alcast Company
Pass away spreading is a fantastic means to get a number of almost similar parts made out of steel. There are a couple of various aluminum alloys that can be used in die spreading, depending on the store.as cast aluminium high pressure pass away casting component for vehicle and electrical devices An alloy, by meaning, is the mix of two or even more products to make a single substance. In this case, it's the process of mixing aluminum with other elements. Alloys will also blend together different material homes of the materials that go into the combination.
In our experience, there are a lot of circumstances where one alloy will certainly work perfectly, and another alloy will fall short catastrophically. An example of this is stamina needs or a material's resistance to rust. Aluminum Casting. If there's inadequate aluminum in the combination, after that the part will not be as solid
The Best Strategy To Use For Alcast Company
Selecting A380 is a wonderful method to conserve money and reduced the overall weight of your part. It's even more of a "general-use" choice that doesn't offer the very same ruggedness or corrosion resistance that alloys have, yet it's more economical and less complicated to work with. Also if you have a detailed get rid of hard geometries, there's a good opportunity that A380 will certainly work throughout the die-casting process.
In spite of the lower price tag, this alloy is still extremely strong, has impressive electrical conductivity, and can resist warm well. With A383 aluminum alloys, you get a lot of the same attributes that A380 has - aluminum foundry. The difference is that A383 is also better at loading molds, so we may suggest this product option if your part is remarkably elaborate
All about Alcast Company
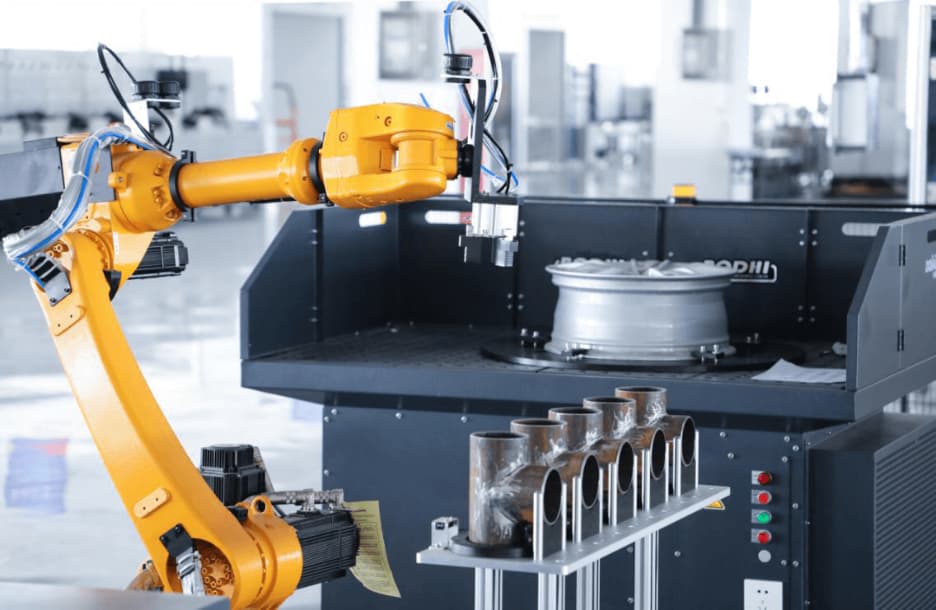
If you have an easier part that calls for greater stamina and you do not mind paying more per device, then A360 may be the most effective option for you. The initial choice we'll point out in the ZA-series (or zinc aluminum alloys) is the ZA-8 aluminum alloy. This choice has a reduced degree of light weight aluminum which equates to a higher density and reduced melting point.
How Alcast Company can Save You Time, Stress, and Money.
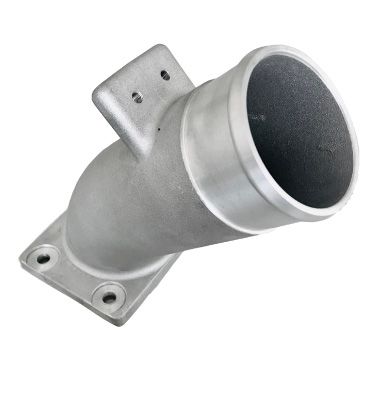
In various other words, we can still function with this alloy without huge problems, and you obtain a component that satisfies every one of your toughness requirements. As we stated ZA-27 has the greatest quantity of aluminum in the ZA-series that is made use of for die casting. Of the three, it's one of the most difficult to cast, so it can only be used for sure projects.
Some Ideas on Alcast Company You Need To Know
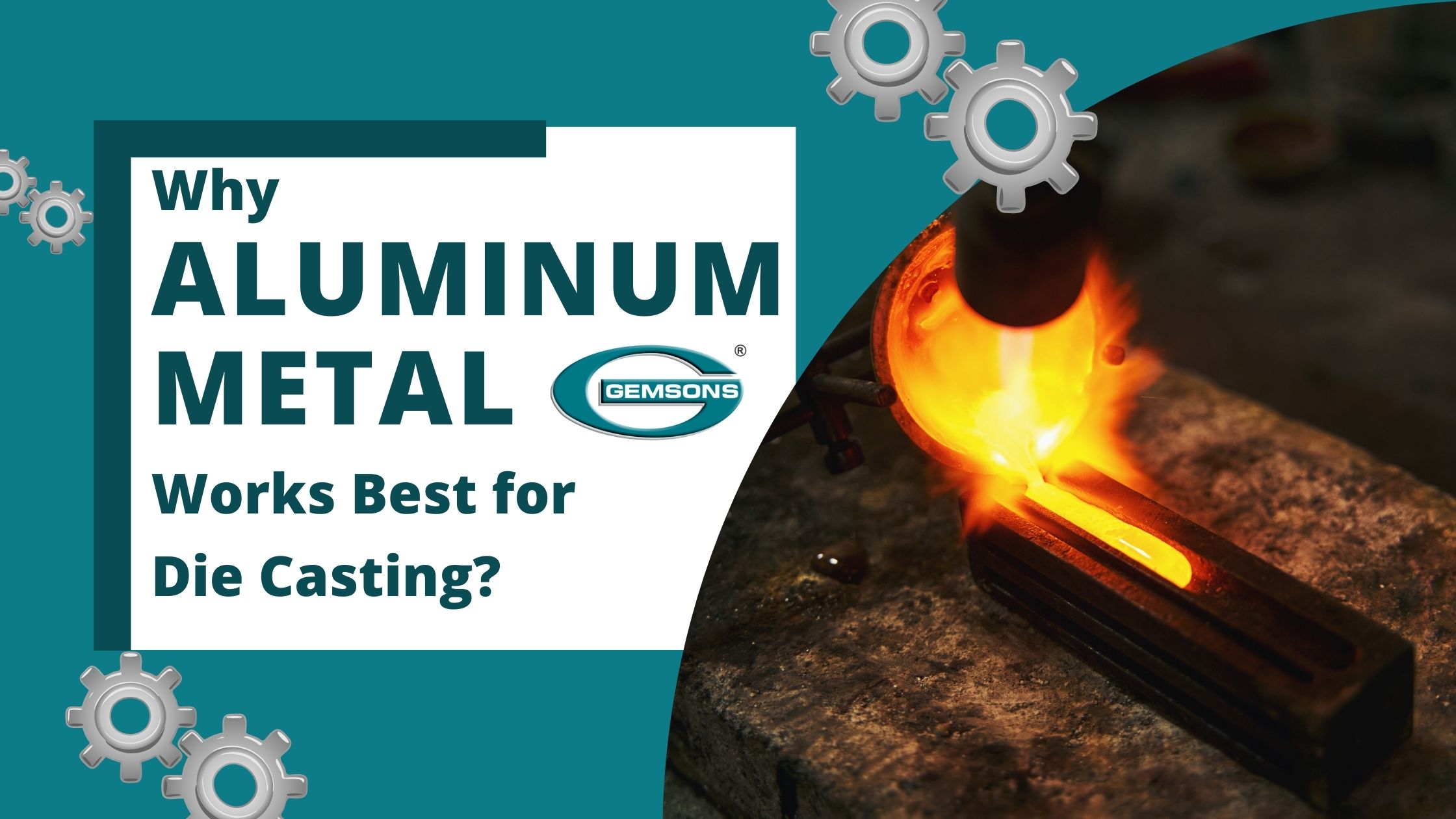
This lost foam spreading is one of a set, that will form incredibly unusual coffee table feet. Do not lose whole lots of time accumulating aluminium beer and soda canisters they can work (forgive the word play here) but there is a fairly strong agreement among casters that they don't work well.
(How Alcast Company can Save You Time, Stress, and Money.
To check, file a little the wheel off and spray the filings in the heater. An alloy extremely high in magnesium will burn a bit like a sparkler. Either stay clear of thawing it entirely or use it very moderately and thoroughly as an alloying component for various other aluminium rich melts.
One downside to alloy wheels, and engine block sized scrap is the need to suffice into little bits that will suit your crucible. Alloys with silicon, like 300 collection aluminium are some of the toughest actors aluminium alloys. Lots of others that people assume of as strong (such as 6000 & 7000 collection alloys) are in fact developed for extrusion or rolling, and do not really achieve their finest residential properties unless cold functioned.
My suggestions nevertheless, is to attempt and begin with excellent scrap castings that are currently a preferable alloy. Naturally, if you currently Discover More have a big stock of scrap extrusion or other non actors Al, go on and find out about alloying it. aluminum metal casting. In terms of locating malfunctions of casting alloys, is an outstanding resource (and not simply for steel homes!)
The Ultimate Guide To Alcast Company
Cast aluminum refers to aluminum alloys that are specifically created for casting procedures such as die spreading, investment casting, gravity spreading, and sand spreading. Cast aluminum refers to light weight aluminum alloys formulated for casting processes like die casting and sand spreading. The essential distinction between cast light weight aluminum and common aluminum depends on their microstructure and properties.
Report this page